Advance Auto Parts Case Study
Case Study: Advance Auto Parts Store Remodels & Conversions
https://advanceautoparts.com/
The DisplayMax team has been working with Advance Auto Parts (AAP) for over 12 years performing a wide range of retail services including store remodels, resets, fixture installation, gondola relocation, merchandising, inventory conversions, and tagging. In 2019, we completed 80 stores in their network of stores.
Typically, our team size range from 4 t0 12 field reps depending upon the specific needs of the project scope. A team effort is essential on their projects because of the demanding nature of merchandising auto parts. It is a unique market in that auto parts come in many different sizes, shapes, packaging, and product weights. In one day, a merchandiser can be handling heavy batteries in the morning, unwieldy exhaust pipes after lunch, and placing small carded screws on 12 feet of peg hooks to finish the day. Attention to detail and perseverance are required to be on an AAP team. Fortunately, we are blessed with dedicated team members who execute these stores to a high standard.
These teams of road warriors are very flexible and experienced at working on a variety of required scopes depending on the store format.
Advance AutoParts Remodel
These usually focus on store reset and merchandising, gondola relocation, tear down and fixture installation. Man of these includes shrinking the sales floor and expanding the parts departments. We also build the new parts department racking behind the counter and stock product. During the remodel, our team leads work with AAP supervisor to delegate tasks to the team.
WorldPac Warehouse
These style of stores have no sales floor and are not open to the public. Typically, we stock products for distribution including inventory scanning products and placing appropriate locations.
Autoparts International
On these projects, our teams help relocate older stores. A key part of the scope on these projects is to demo old fixtures and clean the store out when finished.
Independent Carquest
On Carquest projects, we inventory the entire store, pack up lines of the product getting replaced, bring in new inventory, audit each category of parts, and then inventory on the last day. Carquest sells their brand to small independent store operators and our teams help them convert the inventory to satisfy the contract and to keep their store merchandising sets up to the established standards. On these types of projects, we have the challenge of keeping two clients happy.
Relocations and Conversions
One strategy of AAP is to take Autoparts International stores and convert them to WorldPac locations. These require a completed different tagging model to work within the WorldPac inventory system. Worldpac locations.
The wide range of services required for these type of projects is a welcome challenge to our teams and offer them an opportunity to sharpen and expand their skill set. We are looking forward to the new Advance Auto Parts projects upcoming this year.
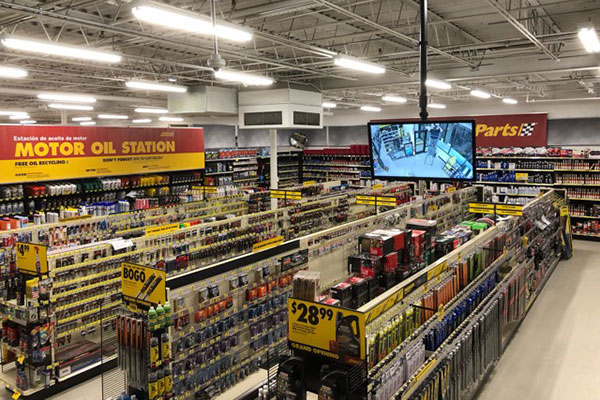
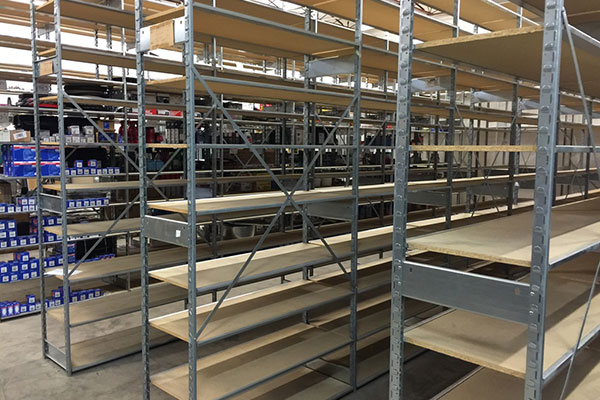
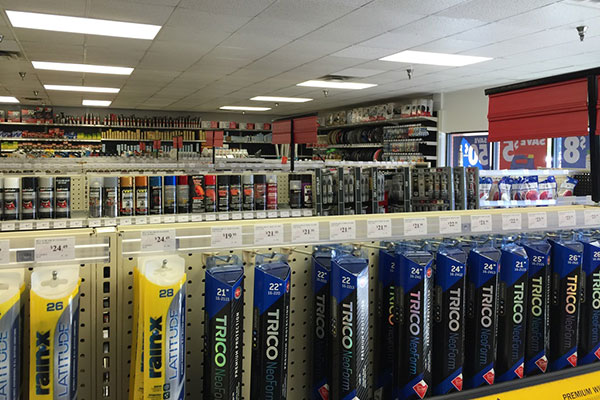
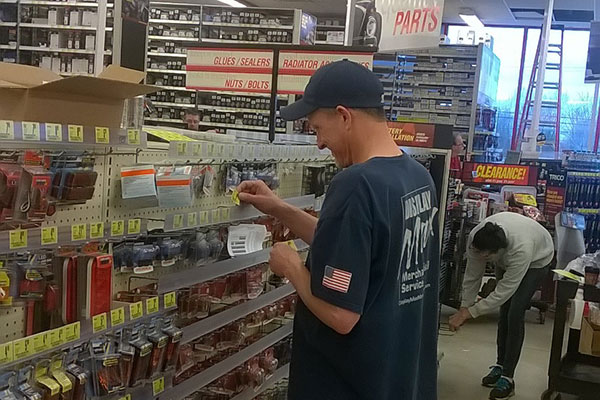
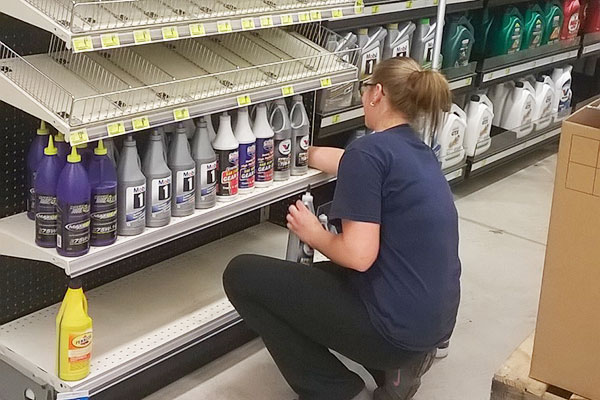
Advance Auto Parts Project Gallery
Tell Us About Your Upcoming Project
Complete the form below if you would like to discuss your project with one of our knowledgable experts, please call 517-545-5540. Or, open a chat box below.